Plumbing involves the installation of piping systems for water supply, drainage, and sewerage. It also includes the fixtures and appliances that use these pipes.
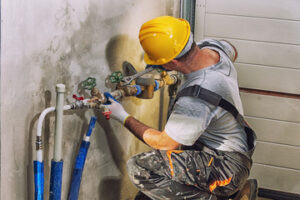
Plumbers can work in a variety of environments, including commercial and industrial settings. They can install, maintain, and repair plumbing equipment. In this article, we’ll explore the basics of plumbing.
The valve seat performs four important functions: sealing when the valve is closed, allowing air to flow freely when open, resisting carbon buildup and providing proper heat transfer. When the seat is not in good condition, it can cause loss of compression or combustion gases and premature wear on other components such as the valve stem and spring, valvetrain or head and piston seals.
The quality of the valve seat depends on material, machining and casting techniques as well as proper mounting. Using an inappropriate material can compromise the valve seat’s function, resulting in loss of airflow, improper valving and valvetrain wear and possibly even head and valve damage.
When the valve seat is worn or leaking, a number of problems can occur, including poor engine performance, loss of power and overheating. The wear is the result of the high frequency opening-and-closing movement that impacts the back of the valve seat against the face of the valve stem. This impact causes the valve seat to degrade, loosen or completely break.
Many aftermarket valve seats are available in a variety of materials, from virgin PTFE to a variety of metal alloys. Many seat suppliers recommend using a seat material best suited to the application. According to Tom Tucker of Tucker Valve Seats, 440 stainless steel seats or silicone XB (an iron seat with 18 percent chrome) are popular for street and mild-performance applications, while a powdered metal valve seat insert is more appropriate for higher load and higher temperature applications.
A properly formed valve seat is a press-fit of an approximately cylindrical piece of a hardened metal alloy into a cast depression in the cylinder head above each eventual valve stem position. The seat is then machined with a conical-section surface that mates with a matching one on the valve stem. The seat should have a slight interference fit and not require locking fluid, peening or staking.
A misaligned valve seat that is not centered with the guide can cause flexing of the seat when the valve closes. This can cause the seat to crack, which can be very difficult to repair. To recondition the head, the counterbore must be remachined to a new size in order to control the interference fit. This will also allow you to better control runout and concentricity of the seat with the valve guide.
Handle
A handle is a piece of material designed to be gripped or held by the hand. It is usually a part of something bigger and may be used to control or guide that thing. Handles are also used as a clue in a mystery.
A handle can be difficult to turn if its internal parts become damaged or misaligned. This can happen during initial installation or during a previous repair.
The first step is to remove the old handle by unscrewing it with a wrench or screwdriver. A replacement can be purchased at the hardware store, but it is important that the length, angle and style of the arm and handle are identical to the original. If the nut that secures the handle has left-handed threads, spray the nut with penetrating oil like WD-40 to loosen it and make it easier to remove with your wrench. This will help prevent the threads from being stripped.
Disc Cartridge
A cartridge system uses a pair of hardened ceramic discs to control water flow. One disc is fixed in place whilst the other moves with the tap handle. A quarter turn of the handle will rotate the discs, allowing or preventing water to flow. The mechanism is very simple and requires little maintenance. The absence of rubber washers means that there are no leaks or dripping, which saves energy and contributes to water conservation. It also eliminates the need for regular replacements, saving money.
Cartridges are resistant to temperature fluctuations, so they can withstand frequent hot and cold changes without degrading or leaking. This allows them to function smoothly and with precise control. Incorporating this technology into bath taps ensures that the faucet operates reliably for its lifespan, enhancing user experience.
A water tap with a disc cartridge also has an advantage over traditional valves. Unlike compression-based mechanisms, which use metal washers to control water flow, the ceramic discs slide against each other, resulting in frictionless movement. This provides an effortless and smooth operation, and allows the user to control temperature and water flow easily and precisely.
Ceramic disc cartridges are also highly durable and resistant to wear. This minimises the need for regular replacements, extending the lifespan of the cartridge and the entire faucet system. The tight seal of the cartridge also reduces the occurrence of leaks and drips, which can lead to unnecessary water wastage. The ceramic material is also non-corrosive and easy to clean, enabling the cartridge to retain its quality over time.
The metal stem at the top of a cartridge has a series of ridges (or splines) that fit into the grooves in the handle. Each spline is measured in points and is designed to match with the corresponding groove on the handle, which ensures that the cartridge fits securely into place.
The first step in repairing a ceramic disc faucet is to locate the cartridge. This can usually be found underneath the sink for a sink faucet and in the wall for a showerhead. Once the cartridge has been removed, examine it for damage or signs of a water leak. The most common reason for a leak is that the rubber seals at the bottom of the cartridge are damaged or layered with grit and mineral deposits. To repair this, remove the cartridge from the faucet body and clean the sealing rings using a nonmetallic nylon brush. Alternatively, a product such as Lime-A-Way can be used to dissolve deposits.
Seals
When it comes to push-fit fittings, the O-ring is one of the most important components. This simple rubber ring makes a seal, preventing water from leaking out of the fitting and saving homeowners money on costly repairs. But this isn’t the only area where O-rings can play a vital role in plumbing.
The plumbing vent system in homes also relies on O-rings to provide a watertight seal and resist internal and external pressures. This vent system ensures that sewage does not back up into sink drains, where it can cause unpleasant and hazardous smells. Homes with insufficient or clogged vent systems often experience the unpleasant sensation of sewer gas smells, which may be caused by the failure of a water seal in the toilet vent.
To create a reliable and long-lasting plumbing seal, it is essential that plumbers use the right types of materials. These include putty compounds, silicone caulking, and o-rings. These materials are able to withstand high temperatures and can help prevent leaks from occurring.
A common o-ring used in plumbing is made of a material known as Viton, which has good resistance to petroleum oils, acids, and other chemicals. This o-ring is commonly found on a variety of plumbing fixtures, including valves, sink strainers, and pop-up drains. In addition to o-rings, plumbers also use other forms of sealing technology when repairing or replacing pipes and other plumbing fixtures.
For example, plumbers often use pipe repair sleeves to create a watertight seal around broken portions of pipe. These sleeves are designed to fit tightly over the damaged portion of pipe and can be purchased at most hardware stores. The sleeves are easy to install and require no special tools.
Before beginning any plumbing work, it is important to turn off the water supply. Look for the shut-off valve under the sink and turn it clockwise until it stops the flow of water. This will protect you from accidental flooding while you work.
Once the water supply is turned off, clear out the storage space under your sink and clean the surface where you plan to apply the putty or sealant. Remove any dust or dirt that may be present, and ensure that the area is free of rust or corrosion. Once the surface is ready, you can begin applying the sealant. Follow the manufacturer’s instructions to get the best results.